Gantry for Cutting Iron Slab
📞 02 9980 7779Gantry for Cutting Iron Slab
Automated, and remotely controlled gantry for slow cutting of steel slab
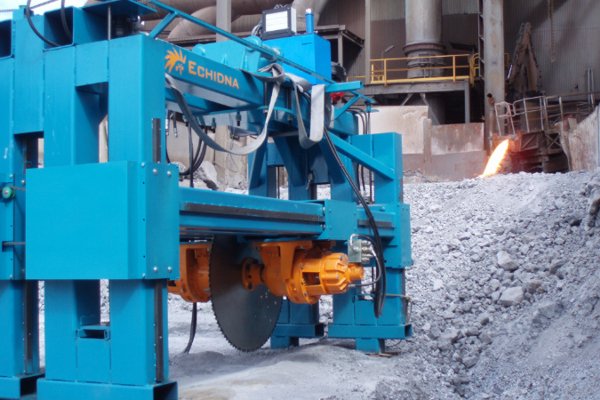
Automated, Self-powered and Remote Controlled Gantry for Bluescope
In July 2008, Echidna Production Machinery was approached to supply a D3 diamond rock saw to cut a large and unwanted iron slab at BlueScope in Port Kembla. Although the saw did cut, the going was slow and it was clear that the diamond saw was not the machine for the job.
What was needed was a specially designed machine that would have a large blade for metal cutting. A test with a small test unit confirmed that this kind of saw did indeed cut the slab.
The problem with this kind of blade, however, is that it is easy to break the tips off, it requires a very steady and constant feed rate and an excavator is not an instrument capable of meeting these requirements.
There were three main issues to be dealt with. Firstly, the blade needed to be lowered gently onto the slab so that the teeth were not torn off on impact. Secondly, the saw needed to be precisely aligned with any previous cuts. Thirdly, the whole unit needed to be absolutely steady and free of vibration.
The design of the machine commenced in August 2008 by Echidna's top engineer and designer, Dr George Fischer. George has a background in materials science, engineering and mining engineering and has been designing and developing a wide range of precision machinery for many years.
The saw blade is driven by two hydraulic motorsr run from the host 45t excavator, geared down by two Sumitomo CycloDrive speed reducers to give an output torque in excess of 40,000 Nm and an absolutely steady speed output of 8 rpm.
The horizontal and vertical movement of the gantry are driven by another set of orbital hydraulic motors that are driven from an auxiliary hydraulic system powered by a diesel motor. The machine is put into position by the excavator and lowered to the ground. From there, the excavator operator can initiate the cut using a radio operated remote control unit from a distance up to 1 km. The saw operates automatically, raising and lowering the blade and driving it forward to progress the cut. When the cut is completed, the saw returns to its starting position and the entire machine is then repositioned by the excavator.
The project was completed in conjunction with Select Civil Pty Ltd who supplied the excavators and operators. The CycloDrive speed reducers were supplied by Sumitomo Drive Technologies in Sydney. The design, construction, assembly and testing were done at Echidna's workshop.
Echidna uses Australian materials and workmanship whereever possible in all of its projects.
Contact Echidna using the form below